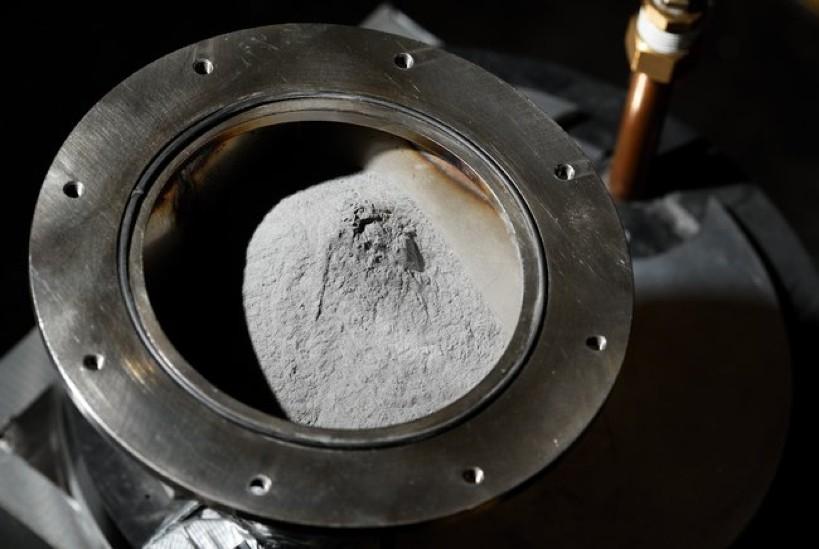
Toekomst in poedervorm
Het Zweedse bedrijf VBN Components produceert staalproducten met behulp van additieve technologieën met behulp van poeder met additieven, voornamelijk gereedschappen zoals boren en frezen. 3D-printtechnologie elimineert de noodzaak voor smeden en machinale bewerking, vermindert het verbruik van grondstoffen en biedt eindgebruikers een ruimere keuze aan hoogwaardige materialen.
Het aanbod van VBN componenten omvat oa. Vibeniet 290wat volgens het Zweedse bedrijf het hardste staal ter wereld is (72 HRC). Het proces van het maken van Vibeniet 290 is om de hardheid van materialen geleidelijk te verhogen tot. Zodra de gewenste onderdelen uit deze grondstof zijn geprint, is er geen verdere bewerking anders dan slijpen of EDM nodig. Snijden, frezen of boren is niet nodig. Zo maakt het bedrijf onderdelen met afmetingen tot 200 x 200 x 380 mm, waarvan de geometrie niet kan worden geproduceerd met andere productietechnologieën.
Staal is niet altijd nodig. Een onderzoeksteam van HRL Laboratories heeft een 3D-printoplossing ontwikkeld. aluminium legeringen met hoge sterkte. Het heet nanofunctionele methode. Simpel gezegd, de nieuwe techniek bestaat uit het aanbrengen van speciale nanofunctionele poeders op een 3D-printer, die vervolgens worden "gesinterd" met een laserdunne laag, wat leidt tot de groei van een driedimensionaal object. Tijdens het smelten en stollen worden de resulterende structuren niet vernietigd en behouden ze hun volledige sterkte doordat de nanodeeltjes fungeren als nucleatiecentra voor de beoogde microstructuur van de legering.
Legeringen met een hoge sterkte, zoals aluminium, worden veel gebruikt in de zware industrie, luchtvaarttechnologie (bijv. romp) en auto-onderdelen. De nieuwe technologie van nanofunctionalisatie geeft ze niet alleen een hoge sterkte, maar ook een verscheidenheid aan vormen en maten.
Optellen in plaats van aftrekken
Bij traditionele metaalbewerkingsmethoden wordt afvalmateriaal machinaal verwijderd. Het additieve proces werkt omgekeerd - het bestaat uit het aanbrengen en toevoegen van opeenvolgende lagen van een kleine hoeveelheid materiaal, waardoor XNUMXD-onderdelen van bijna elke vorm worden gemaakt op basis van een digitaal model.
Hoewel deze techniek al veel wordt gebruikt voor zowel prototyping als modelgieten, was het moeilijk om het rechtstreeks in de productie van goederen of apparaten voor de markt te gebruiken vanwege de lage efficiëntie en onbevredigende materiaaleigenschappen. Deze situatie verandert echter geleidelijk dankzij het werk van onderzoekers in veel centra over de hele wereld.
Door nauwgezette experimenten zijn de twee belangrijkste technologieën van XNUMXD-afdrukken verbeterd: laserdepositie van metaal (LMD) ik selectief lasersmelten (ULM). Lasertechnologie maakt het mogelijk om nauwkeurig fijne details te creëren en een goede oppervlaktekwaliteit te verkrijgen, wat niet mogelijk is met 50D elektronenstraal printen (EBM). Bij SLM wordt de punt van de laserstraal op het poeder van het materiaal gericht en lokaal volgens een bepaald patroon gelast met een nauwkeurigheid van 250 tot 3 micron. LMD gebruikt op zijn beurt een laser om het poeder te verwerken tot zelfdragende XNUMXD-structuren.
Deze methoden zijn veelbelovend gebleken voor het maken van vliegtuigonderdelen. en met name laserdepositie van metaal vergroot de ontwerpmogelijkheden voor ruimtevaartcomponenten. Ze kunnen worden gemaakt van materialen met complexe interne structuren en hellingen die in het verleden niet mogelijk waren. Bovendien maken beide lasertechnologieën het mogelijk om producten met een complexe geometrie te creëren en uitgebreide functionaliteit van producten te verkrijgen uit een breed scala aan legeringen.
Afgelopen september maakte Airbus bekend dat het zijn productie A350 XWB had uitgerust met additief printen. titanium beugel, vervaardigd door Arconic. Dit is niet het einde, want het contract van Arconic met Airbus voorziet in 3D-printen van titanium-nikkelpoeder. lichaamsdelen i aandrijfsysteem. Er moet echter worden opgemerkt dat Arconic geen lasertechnologie gebruikt, maar een eigen verbeterde versie van de EBM elektronische boog.
Een van de mijlpalen in de ontwikkeling van additieve technologieën in de metaalbewerking is waarschijnlijk het allereerste prototype dat in het najaar van 2017 op het hoofdkantoor van de Nederlandse Damen Shipyards Group wordt gepresenteerd. scheepsschroef metaallegering vernoemd naar VAAMPeller. Na passende tests, waarvan de meeste al hebben plaatsgevonden, maakt het model kans om te worden goedgekeurd voor gebruik aan boord van schepen.
Aangezien de toekomst van de metaalbewerkingstechnologie ligt in roestvaststalen poeders of legeringscomponenten, is het de moeite waard om kennis te maken met de belangrijkste spelers op deze markt. Volgens het "Additive Manufacturing Metal Powder Market Report", gepubliceerd in november 2017, zijn de belangrijkste fabrikanten van metaalpoeders voor 3D-printen: GKN, Hitachi Chemical, Rio Tinto, ATI Powder Metals, Praxair, Arconic, Sandvik AB, Renishaw, Höganäs AB , Metaldyne Performance Group, BÖHLER Edelstahl, Carpenter Technology Corporation, Aubert & Duval.
WAAMpeller propeller print
Vloeibare fase
De meest bekende metaaladditieventechnologieën zijn momenteel afhankelijk van het gebruik van poeders (zo wordt het bovengenoemde vibenite gemaakt) "gesinterd" en lasergesmolten bij de hoge temperaturen die nodig zijn voor het uitgangsmateriaal. Er ontstaan echter nieuwe concepten. Onderzoekers van het Cryobiomedical Engineering Laboratory van de Chinese Academie van Wetenschappen in Peking hebben een methode ontwikkeld 3D printen met "inkt", bestaande uit een metaallegering met een smeltpunt iets boven kamertemperatuur. In een studie gepubliceerd in het tijdschrift Science China Technological Sciences demonstreren onderzoekers Liu Jing en Wang Lei een techniek voor het printen in de vloeistoffase van gallium-, bismut- of indium-gebaseerde legeringen met toevoeging van nanodeeltjes.
Vergeleken met traditionele methoden voor metaalprototyping heeft 3D-printen in vloeibare fase verschillende belangrijke voordelen. Ten eerste kan een relatief hoge fabricagesnelheid van driedimensionale structuren worden bereikt. Bovendien kunt u hier de temperatuur en het debiet van de koelvloeistof flexibeler aanpassen. Daarnaast kan vloeibaar geleidend metaal worden gebruikt in combinatie met niet-metalen materialen (zoals kunststoffen), wat de ontwerpmogelijkheden voor complexe componenten vergroot.
Wetenschappers van de American Northwestern University hebben ook een nieuwe metalen 3D-printtechniek ontwikkeld die goedkoper en minder complex is dan voorheen bekend was. In plaats van metaalpoeder, lasers of elektronenstralen, gebruikt het conventionele oven i vloeibaar materiaal. Bovendien werkt de methode goed voor een breed scala aan metalen, legeringen, verbindingen en oxiden. Dit is vergelijkbaar met de mondstukafdichting die we kennen van kunststoffen. "Inkt" bestaat uit een metaalpoeder opgelost in een speciale stof met toevoeging van een elastomeer. Op het moment van aanbrengen is het op kamertemperatuur. Daarna wordt de laag materiaal die uit het mondstuk wordt aangebracht, gesinterd met de vorige lagen bij een verhoogde temperatuur die in de oven wordt gecreëerd. De techniek wordt beschreven in het gespecialiseerde tijdschrift Advanced Functional Materials.
Chinese vloeibare metaalfase-afdrukmethode
In 2016 introduceerden Harvard-onderzoekers een andere methode waarmee XNUMXD-metaalstructuren kunnen worden gemaakt. gedrukt "in de lucht". Harvard University heeft een 3D-printer gemaakt die, in tegenstelling tot anderen, geen objecten laag voor laag creëert, maar complexe structuren "in de lucht" creëert - van metaal dat onmiddellijk bevriest. Het apparaat, ontwikkeld aan de John A. Paulson School of Engineering and Applied Sciences, print objecten met zilveren nanodeeltjes. De gerichte laser verwarmt het materiaal en versmelt het, waardoor verschillende structuren ontstaan, zoals een helix.
De marktvraag naar zeer nauwkeurige 3D-geprinte consumentenproducten zoals medische implantaten en vliegtuigmotoronderdelen groeit snel. En omdat productgegevens met anderen kunnen worden gedeeld, kunnen bedrijven over de hele wereld, als ze toegang hebben tot metaalpoeder en de juiste 3D-printer, de logistiek en voorraadkosten verlagen. Zoals bekend vergemakkelijken de beschreven technologieën de vervaardiging van metalen onderdelen met een complexe geometrie aanzienlijk, in tegenstelling tot traditionele productietechnologieën. De ontwikkeling van gespecialiseerde toepassingen zal waarschijnlijk leiden tot lagere prijzen en openheid voor het gebruik van 3D-printen in conventionele toepassingen.
Het hardste Zweedse staal - voor 3D-printen:
Het hardste staal ter wereld - gemaakt in Uppsala, Zweden
Aluminiumfolie om af te drukken:
Doorbraak in de metallurgie: 3D-printen van hoogwaardig aluminium

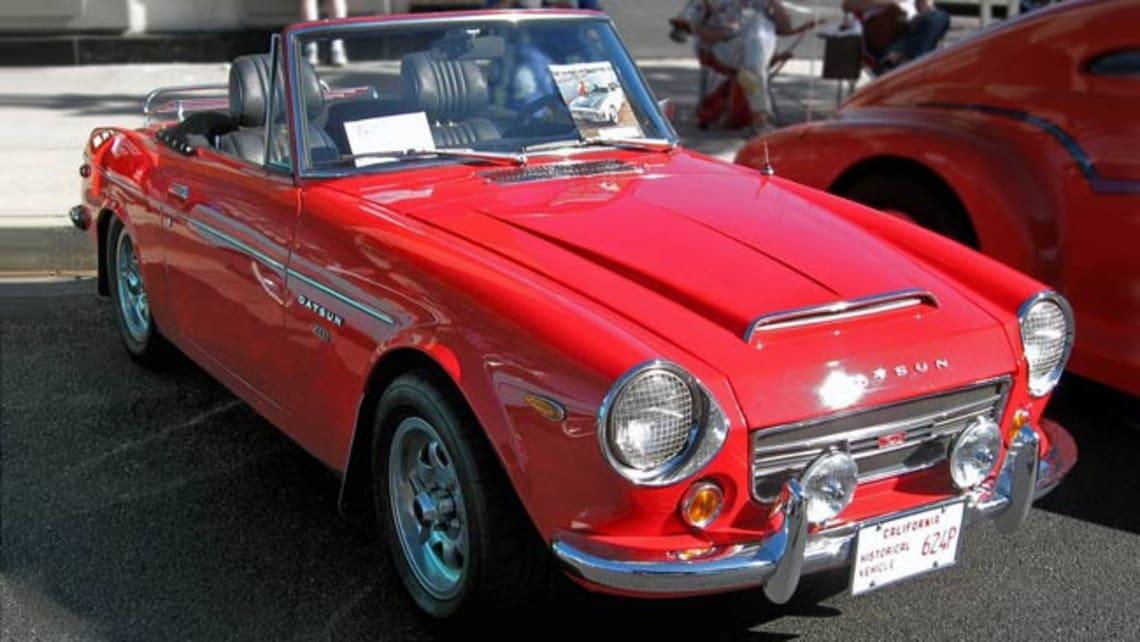
Een commentaar
anonymus
Grap