
Hier zijn de echte redenen waarom de wachttijden voor de Toyota LandCruiser, Kia Sorento en andere nieuwe 2022-voertuigen nog steeds erg lang zijn.
Inhoud

Van chips tot schepen tot zieke werknemers, er zijn verschillende redenen waarom u het onmogelijk vindt om een Land Cruiser te kopen.
Heb je al geprobeerd een nieuwe auto te kopen? Voor sommige modellen, zoals de Toyota Landcruiser 300 en RAV4 of Volkswagen Amarok, moet u vele maanden wachten, mogelijk tot zes maanden of zelfs langer, om veelgevraagde opties te krijgen.
Denk je dat je dit kunt vermijden door in plaats daarvan iets te weinig gebruikt te kopen? In zekere zin is dit het ergste wat je kunt doen. De markt voor gebruikte auto's heeft kennis genomen van het tekort aan nieuwe auto's, en zowel particuliere verkopers als dealers van tweedehands auto's geven zich over aan ouderwetse prijsopdrijving, vooral op SUV's en SUV's. Overweegt u een Suzuki Jimny te kopen op de markt voor gebruikte auto's? Doe dit niet tenzij u bereid bent een premie van vijf cijfers te betalen ten opzichte van de detailhandel.
Maar waarom zijn er twee jaar na het begin van de pandemie nog steeds zo weinig auto's? Is de pandemie nog steeds de schuld? Het antwoord is simpel: "omdat computerchips"? Oh nee. De situatie is iets gecompliceerder, maar om te begrijpen waarom, moeten we eerst begrijpen hoe toeleveringsketens in de auto-industrie werken.
Een keten van zwakke schakels
Alles is verbonden. Alle. Er is ook geen speling in de wereldwijde toeleveringsketen. Wanneer de leverancier zijn deel van deze metaforische keten verlaat, voelt de consument dat ook aan zijn kant.
Veel hiervan heeft te maken met de industriepraktijk die bekend staat als just-in-time productie, ook wel bekend als lean manufacturing. Voor het eerst ontwikkeld door Toyota in de eerste helft van de vorige eeuw en sindsdien overgenomen door vrijwel elke autofabrikant, heeft het autofabrikanten in staat gesteld om af te stappen van het aanhouden van grote voorraden van onderdelen, assemblages en grondstoffen en in plaats daarvan ervoor te zorgen dat de hoeveelheid bestelde onderdelen van leveranciers komt overeen met hun hoeveelheid. onderdelen die daadwerkelijk nodig zijn om auto's te produceren, niet meer en zeker niet minder. Het elimineerde verspilling, leidde tot een veel efficiëntere toeleveringsketen, verhoogde fabrieksproductiviteit, en als alles naar behoren werkt, is het praktisch de beste manier om auto's bij elkaar te krijgen tegen een betaalbare prijs.
Dit is echter geen systeem dat bijzonder goed bestand is tegen storingen.
Om het risico te minimaliseren dat de hele assemblagelijn wordt stilgelegd omdat één leverancier niet kan samenwerken, zullen autofabrikanten dus de zogenaamde "multisourcing" gebruiken. Van banden tot afzonderlijke moeren en bouten, een component heeft zelden slechts één bron, en vaak zijn er meerdere als het onderdeel op grote schaal wordt gebruikt op een productielijn voor meerdere modellen. De eindconsument weet niet of het plastic voor zijn deuren is geleverd door leverancier A of door leverancier B - kwaliteitscontrole zorgt ervoor dat ze er allemaal hetzelfde uitzien en hetzelfde aanvoelen - maar dit betekent dat als leverancier A problemen heeft met hun eigen assemblagelijn, leverancier B kan ingrijpen. en zorg ervoor dat er genoeg deurplastic naar de autofabriek gaat om de lijn open te houden.
Leveranciers A en B staan bekend als "Tier XNUMX-leveranciers" en voorzien de autofabrikant rechtstreeks van afgewerkte onderdelen. Er kunnen echter grote problemen ontstaan wanneer al deze eerstelijnsaanbieders dezelfde aanbieder gebruiken hun grondstoffen, die bekend zal staan als tweedelijnsleverancier.
En dat is eigenlijk de situatie als het gaat om zo ongeveer alles wat elektronisch is in een auto. Als een auto-onderdeel een microprocessor van welke aard dan ook vereist, dan zijn de bronnen van siliciumchips waaruit deze microprocessors bestaan belachelijk gecentraliseerd. In feite is slechts één land, Taiwan, goed voor het leeuwendeel van siliciumchips (of halfgeleiders), met maar liefst 63 procent van de wereldwijde markt voor basismaterialen voor halfgeleiders, waarvan de overgrote meerderheid afkomstig is van één bedrijf: TMSC. Als het gaat om de productie van afgewerkte chips en elektronica, hebben de VS, Zuid-Korea en Japan het grootste marktaandeel, en slechts een handvol bedrijven in deze regio's leveren microprocessors aan bijna de hele wereld.
Toen tweederangs leveranciers van microprocessors langzamer gingen werken vanwege de pandemie, deden hun klanten dat natuurlijk ook – al die eersterangs leveranciers. Vanwege het gebrek aan diversiteit aan dit uiteinde van de toeleveringsketen, waren meerdere inkooppraktijken niet voldoende om de assemblagelijnen van 's werelds autofabrikanten draaiende te houden.
De situatie is verslechterd omdat autofabrikanten er niet in slaagden te anticiperen op de aanhoudend grote vraag naar auto's tijdens de pandemie, maar zelfs nu sommige autofabrikanten afstand nemen van auto's om het aantal benodigde chips te verminderen (Suzuki Jimny, Tesla Model 3 en Volkswagen Golf R twee recente voorbeelden) er zijn andere factoren...
De situatie met het schip
Over fragiele ecosystemen gesproken, de wereld van de wereldwijde scheepvaart is net zo vol als de autoproductie.
Niet alleen zijn de winstmarges op zeevervoer verrassend klein, maar containerschepen zijn ook ongelooflijk duur in gebruik. Nu de pandemie de toeleveringsketens heeft verstoord, maar ook een onverwachte vraag naar consumptiegoederen heeft doen ontstaan, is de stroom van schepen en containers ernstig verstoord, wat niet alleen tot enorme vertragingen heeft geleid, maar ook tot hogere verzendkosten.
Het grootste deel van de consumptiegoederen komt uit China en Zuidoost-Azië, en wanneer goederen van dat deel van de wereld naar een ander worden verscheept, worden de containers die die lading vervoeren meestal opnieuw gevuld met producten uit het land van bestemming en opnieuw geladen naar een ander land. Een schip dat uiteindelijk terugkeert naar Zuidoost-Azië om de cyclus opnieuw te voltooien.
Echter, door de grote vraag naar goederen van Chinese makelij, maar een beperkte vraag naar goederen die de andere kant op gaan, belandde een hele reeks containers in havens in Amerika en Europa, en de schepen voeren vervolgens met weinig geld terug naar Azië. of geen lading aan boord. Dit verstoorde de distributie van containers over de hele wereld, wat leidde tot een tekort aan containers in China, wat vervolgens leidde tot enorme vertragingen bij de verzending van alles wat in deze regio wordt geproduceerd - zowel consumptiegoederen als grondstoffen, waarvan sommige nodig waren op productielijnen auto's.
En aangezien moderne productielijnen alleen draaien als onderdelen net op tijd worden geleverd, zorgt dit er natuurlijk voor dat veel assemblagefabrieken inactief blijven wachten op de aankomst van componenten en materialen - componenten en materialen die niet noodzakelijkerwijs tot de eersten behoren. met chips erin.
Je kunt thuis geen auto bouwen
Als u een bediende bent, is de thuiswerkmodus waarschijnlijk een zegen. Als je voor je werk met gereedschap moet werken in een auto-assemblagefabriek, nou... het is niet zo dat je een Kluger in elkaar kunt zetten op je keukentafel.
Ondanks dit hebben veel industrieën met name kunnen blijven werken tijdens de pandemie, maar hoewel fabrieksarbeiders in veel delen van de wereld nog steeds met tools kunnen werken, is er nog steeds een zekere mate van onderbreking in hun workflow.
Ten eerste moesten bedrijven werkplekken veilig genoeg maken voor hun werknemers. Dat betekent werkplekken herconfigureren om social distancing mogelijk te maken, schermen installeren, persoonlijke beschermingsmiddelen bestellen, pauzeruimtes en kleedkamers reorganiseren - de lijst gaat maar door. Dit proces kost tijd. Werken in ploegen met minder personeel is ook een andere strategie geweest voor de veiligheid van werknemers, maar heeft ook een impact op de productiviteit.
En wat gebeurt er dan als er een flits is. De laatste onderbrekingen in de productie van Toyota waren voornamelijk te wijten aan het feit dat arbeiders ziek werden: slechts vier gevallen waren genoeg om de fabriek van het bedrijf in Tsutsumi, Japan, te sluiten. Zelfs als fabrieken niet sluiten wanneer iemand ziek wordt, heeft het ziekteverzuim van werknemers als gevolg van quarantaine nog steeds invloed op de productiviteit van de fabriek vanwege de wijdverbreide verspreiding van het COVID-19-virus.
Dus... wanneer zal het eindigen?
Er is niet één centrale reden waarom auto's nu moeilijk te krijgen zijn, maar er zijn veel onderling verbonden redenen. Het is gemakkelijk om COVID-19 de schuld te geven, maar de pandemie was slechts een trigger die ervoor zorgde dat het kaartenhuis, d.w.z. de wereldwijde toeleveringsketen voor auto's, instortte.
Maar uiteindelijk wordt alles hersteld. Er is veel traagheid in zaken als de fabricage van microprocessors en wereldwijde verzending, maar de vooruitzichten op herstel zijn goed. Het valt echter nog te bezien hoe de industrie zichzelf zal isoleren van een herhaling van dit scenario.
Wanneer het herstel zal plaatsvinden, is het onwaarschijnlijk dat dit dit jaar zal gebeuren. Kortom, als u het zich kunt veroorloven om wat langer te wachten met het kopen van uw volgende auto, bespaart u mogelijk geld en verkort u uw wachttijd. Wat er ook gebeurt, geef niet toe aan deze flagrante speculanten op de secundaire markt.

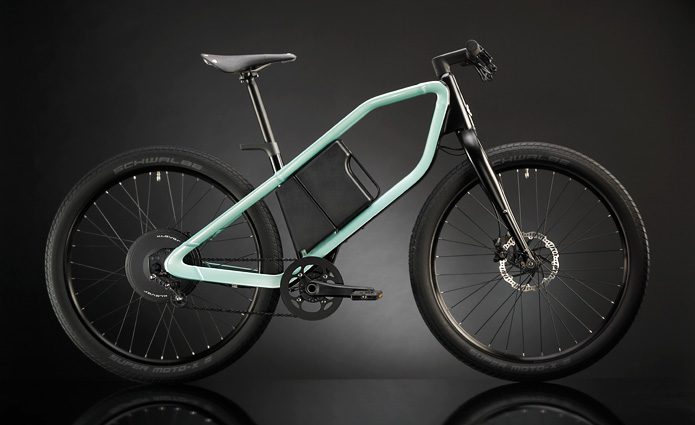